Location & Language Selector
Please select location or visit OUR GLOBAL MERIDA WEBSITE
ALUMINIUM TECHNOLOGY
CUTTING EDGE ALUMINIUM FRAMES
We have produced cutting edge aluminium frames for many years, continually refining our knowledge and developing new technologies. We take great care in selecting or, in some cases, developing grades of aluminium appropriate to the demands of each bike we manufacture. For example, 6016 aluminium enables super thin wall thicknesses with amazing strength, ideal for demanding off-road riding and racing. 6066 aluminium is extremely light and durable, allowing manipulation to create the best possible stiffness to weight ratio. 6061 is the minimum grade we use, developed for the aerospace industry, enabling the production of lightweight and highly advanced frames. The way aluminium is treated and manipulated is as crucial as the grade selection. There are a number of processes involved:
DOUBLE AND TRIPLE BUTTING
Double butting describes tubes with two wall thicknesses; thicker at the ends and thinner in the middle. Triple butting describes tubes with three different wall thicknesses along their length, optimising strength where it is needed but minimising weight in areas subjected to less stress. All our aluminium is heat treated. Frames are heated to very high temperatures (a T6 temper) then quickly cooled in water or oil to ensure the alloying elements don’t precipitate. Frames are subsequently heated to a lower temperature, artificially ageing and significantly strengthening them.
HYDRO AND TECHNOFORMING
Hydroforming involves the insertion of tubes into negative moulds. A hot emulsion of water and oil is forced through at pressure, enabling them to be formed into complex shapes. Technoforming is a mechanical forming process, shaping the tubes by using negative moulds, at times combined with an internal metal core. Smooth welding, also known as double pass welding, refers to a second pass over the weld providing a clean organic look to the frame; at first glance, you will be convinced it is carbon, not aluminium.
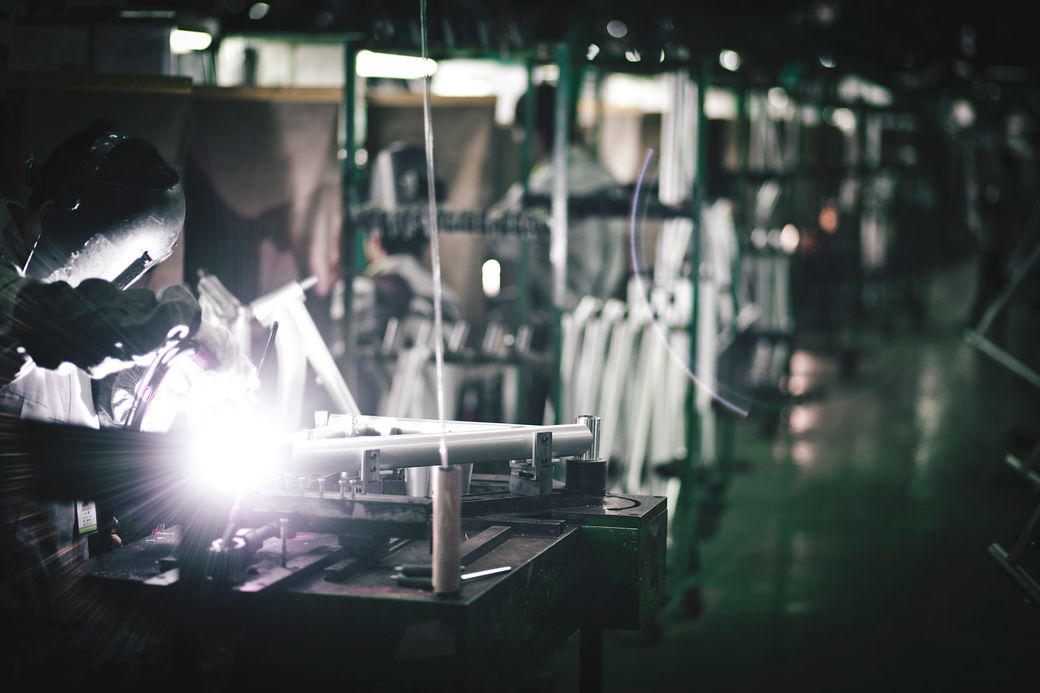